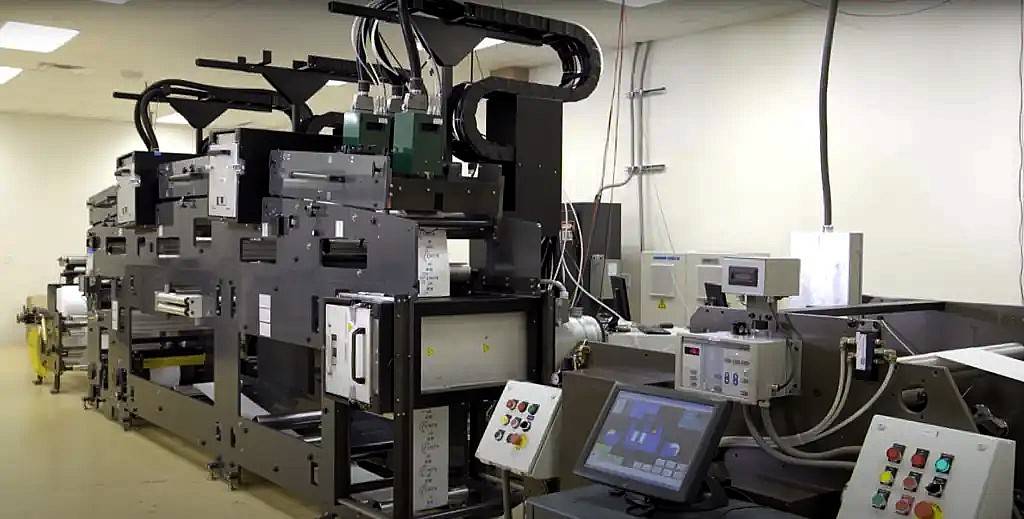
In printing technology, upgrading and modernizing existing equipment is critical. For companies using aging Versamark print modules, retrofitting with X-BAR technology presents a cost-effective opportunity to enhance print capabilities, improve efficiency, and stay competitive in a dynamic market.
Versamark: A Legacy of Digital Printing Performance
Kodak’s Versamark print modules are known for their reliability, quality, and versatility. These modules have served printing companies well, delivering consistent results for producing direct mail, transactional documents, packaging, and labels.
As technology advances and customer demands evolve, aging Versamark printers may struggle to maintain quality standards. Downtime and maintenance costs may also increase.
The Benefits of Retrofitting with X-BAR
Retrofitting aging Versamark print modules with X-BAR technology offers printing companies many benefits and opportunities.
- Compatibility and Integration: X-BAR technology is designed to integrate easily with existing Kodak Versamark systems by replacing existing print modules. This compatibility ensures a smooth transition and minimizes disruptions to production workflows.
- Enhanced Print Quality: X-BAR technology delivers advanced printing capabilities to aging Versamark systems, improving print quality, color accuracy, and resolution. Upgrades with X-BAR print modules allow companies to meet the growing demands for high-quality prints in various applications.
- Efficiency and Productivity: X-BAR retrofitting streamlines production processes, reduces downtime, and improves overall efficiency. By leveraging modern print technologies and software solutions, companies can achieve faster turnaround times and increased productivity.
- Cost-Effective Upgrade: Retrofitting with X-BAR technology is a cost-effective alternative to investing in new printing systems. It allows companies to leverage their existing infrastructure while gaining significant improvements in print capabilities and performance.
X-BAR Technical Specs
4.7” Print Width | 9.4” Print Width | |
Print Array | 2 Arrays of 3 Samba G3L Printheads |
1 Array of 6 Samba G3L printheads |
Nozzles per Array | 5,632 | 11,264 |
Cross Process dpi | 1200 | 1200 |
Process Resolution | 300/600/600i/1200 dpi | 300/600/1200 dpi |
Dimensions and Weight |
– Height 20” – Depth 7.5” – Width 7.5” – 45 lbs |
– Height 11.8” – Depth 9.3” – Width 16” – 54 lbs |
Fluid Station Dimensions and Weight | – Height 40” – Depth 26” – Width 24” – 200 lbs |
– Height 40” – Depth 26” – Width 24” – 200 lbs |
Monochrome System | Black, Spot color | Black, Spot color |
Speed | 1000 fpm @ 1200 x 600 dpi |
1000 fpm @ 1200 x 300 dpi |
Variable Data | Yes | Yes |
X-BAR and Versamark Integration through Universal Controller
When you upgrade to X-BAR, there’s no need for a separate controller for existing Versamark print modules.
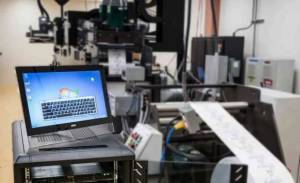
The Universal Controller delivers the future of high-quality inkjet printing as the reliable backbone powering Fujifilm Samba G3L-based X-BAR, Kodak Versamark, and other printing systems.
The Kao Collins Universal Controller integrates with Versamark technology, allowing easy upgrades and enhancements without extensive reconfiguration, software licensing fees, or dongles.
The Universal Controller’s advanced software capabilities, combined with a familiar interface, enable precise control and customization of printing parameters, including waveforms. This level of control ensures optimal print quality and consistency.
Another feature of the Universal Controller is its real-time monitoring and diagnostics functionality. Operators can monitor ink levels, printhead status, and printing performance in real-time, allowing for proactive maintenance and troubleshooting to minimize downtime and maximize productivity.
Universal Controller Features
- No Licensing Fees: Say goodbye to ongoing costs with no licensing fees or dongles required.
- Future-Ready: Continuous development promises additional features like Ink Usage Estimation and Historical Log Support.
- Compatibility: The Universal Controller operates X-BAR and VERSAMARK DS6240 printheads, reducing the need for multiple controllers.
- Read and Print: The controller’s Read and Print feature simplifies operations and requires minimal training, akin to Kodak’s 410 controller.
- GUI Interface: A user-friendly graphical interface represents web-like functionality directly on the controller, enhancing accessibility.
- Tach and Cue Board: This feature ensures precise control and synchronization with up to 8 inputs and 32 outputs.
- Alignment: Kao Collins’s proprietary synchronization technology ensures accurate document alignment across multiple printheads.
The Retrofitting Process
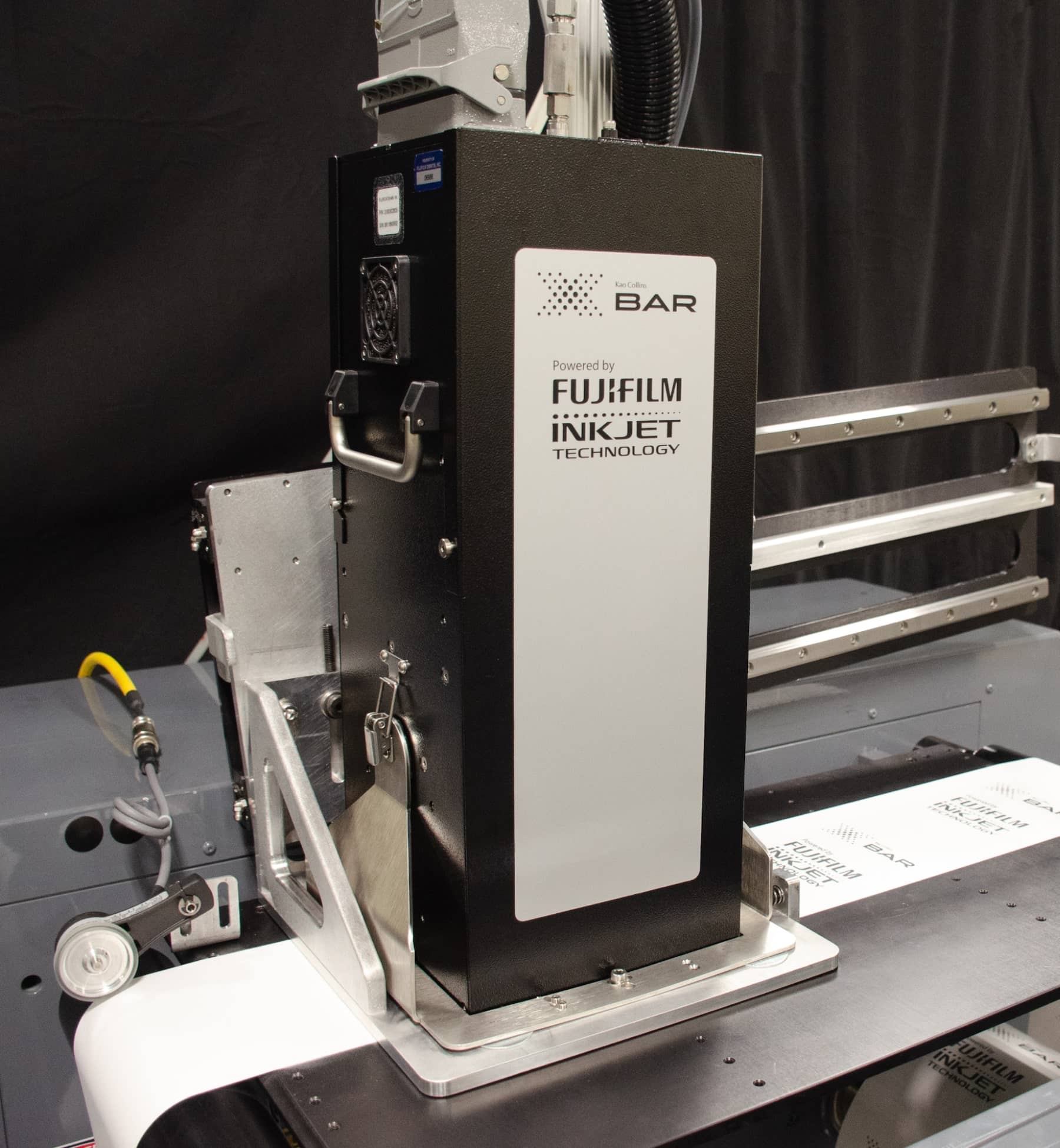
Kao Collins designed the X-BAR print module as a drop-in replacement for Kodak Versamark 6240 modules.
Initially, the X-BAR print module was designed to retrofit the aging Versamark print modules directly. The process involves these critical steps:
- Assessment and Compatibility Check: The existing Versamark print modules are thoroughly assessed to determine compatibility with X-BAR technology. This includes evaluating hardware, software, connectivity options, and integration requirements.
- Installation of X-BAR Print Modules: X-BAR print modules, software solutions, and necessary components are installed and integrated into the existing Versamark systems. This may involve hardware upgrades, firmware updates, and calibration processes to ensure optimal performance.
- Testing and Calibration: After installation, comprehensive testing and calibration are performed to validate the functionality and performance of the retrofitted systems. This includes print quality tests, color calibration, variable data printing tests, and software compatibility checks.
- Training and Optimization: Training sessions are conducted to familiarize operators and staff with the new X-BAR capabilities and workflows. Optimization strategies are implemented to maximize efficiency, reduce waste, and enhance print output.
- Ongoing Support and Maintenance: X-BAR retrofitting includes ongoing support, maintenance, and updates to ensure continued performance and reliability. This provides access to technical support, software upgrades, and troubleshooting assistance as needed.
Future-Proofing Your Printing Infrastructure
Retrofitting aging Versamark print modules with X-BAR technology is a strategic investment in future-proofing your printing infrastructure. It allows companies to leverage the reliability of Versamark systems while gaining access to advanced print capabilities, improved efficiency, and enhanced productivity.
X-BAR arrives at a critical time for companies that rely on Versamark printing systems.
For more details about the X-BAR print module and Universal Controller, you can contact Kao Collins. You can also see X-BAR and the Universal Controller at drupa 2024.
Frequently Asked Questions
X-BAR is a retrofit technology designed to modernize and enhance existing printing systems, improving print quality, efficiency, and productivity while extending the lifespan of the equipment.
Retrofitting with X-BAR technology ensures that your printing systems remain competitive by incorporating advanced print capabilities, improving efficiency, and enhancing productivity, thus extending the life and performance of your existing Versamark systems.