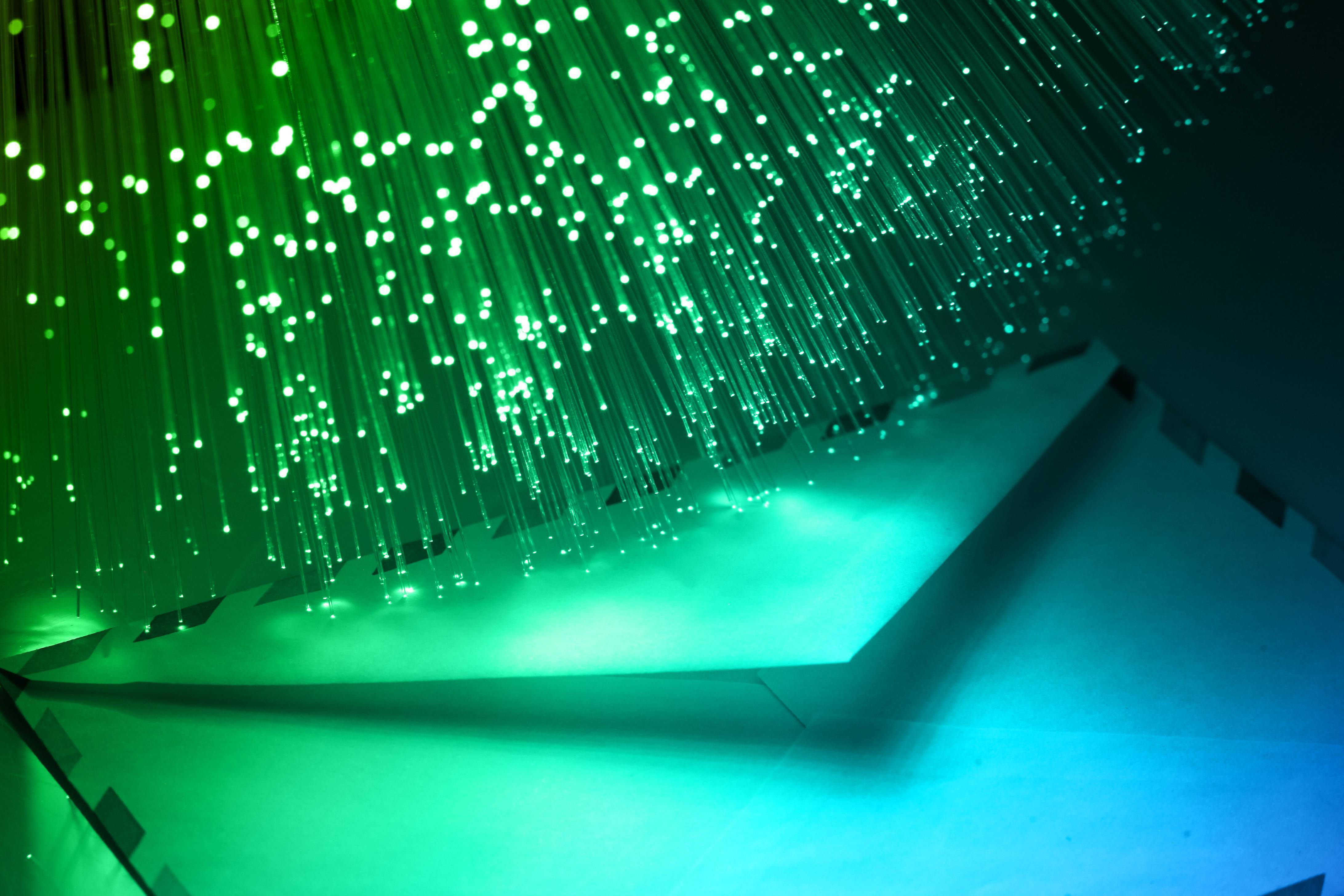
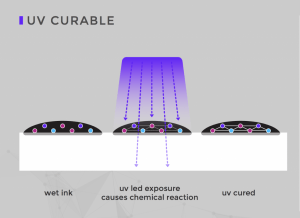
UV Curable Ink – An ultraviolet light source reacts with photoinitiators in the ink solution to cause curing to bond to the substrate.
Solvent-free Ultraviolet light (UV) and Electron beam (EB) inkjet inks cure incredibly fast when exposed to a UV or EB source. These inks eliminate the need for large baking ovens for traditional paints and inks. The technology possesses inherent advantages over solvent and water-based materials as well. UV and EB curing inks have low or zero VOCs, and are considered to be the best achievable control technology.
Difference in Energy
To better understand UV and EB energy, it is essential to consider that their foundations are fundamentally different. For UV energy, the basic piece of the energy utilized is the photon.
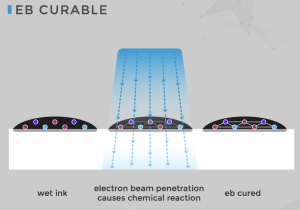
EB Curable Ink Curing – Electron beams cause a reaction with the ink to cause curing to bond the inkjet ink solution to the substrate. It uses significantly less energy than UV curing.
Photons, possessing both particle and wave-like characteristics, have their energy determined by their wavelength.
For applications involving UV curing, the range of wavelengths is usually between 250 and 450 nanometers.
We generally measure UV processes by examining the total amount of energy applied per unit surface area, commonly called the irradiance.
The exact amount of this energy needed varies from project to project and depends on the material and the application. The “dose” in UV curing refers to the energy density; Both dose and irradiance are required for specifying UV curing system.
Whereas photons are the basis of UV energy, EB energy finds electrons at the heart of its procedure. The energy of electrons produced during these operations is determined by the accelerating potential found in the EB equipment being used. For most EB applications, this range usually falls between 80 and 180 kilovolts.
Processes are measured by examining the amount of energy absorbed per unit mass of the substrate, also called the cure dose. Much like the UV operations, the dose needed during an EB procedure depends on both the material and the application.
It is important to note that UV dose is commonly measured in mJ/cm2. Meanwhile, EB curing dose is commonly measured in Mrad.
Penetration of Materials
We can help you decide whether UV or EB ink is better for printing on your substrate.
The type of energy used determines how exactly it penetrates through a material, creating the finished product. Only through effective exposure can an item be appropriately cured. When it comes to UV energy, penetration depends on the optical density of the material being cured. For instance, transparent materials are easier for UV energy to penetrate. This process becomes increasingly difficult when dealing with optically opaque materials, making UV curing through black or metallic materials more challenging. Controlling the penetration of UV energy can be managed by the peak irradiance of the lamp being used, specifically the power and focus of the UV lamp. The ability to cure optically dense materials would, therefore, require a system of powerful, tightly focused lamps.
Read More: Electron-Beam Inks: A Versatile Alternative to UV?
EB penetration, on the other hand, depends on the material’s mass density and thickness as opposed to optical density. Low-density materials are easier for electrons to penetrate than high-density materials. As the electrons are not affected by optical density, the use of EB is effective when dealing with darker or metallic materials. The accelerating potential of the EB equipment controls the penetration and curing.
Equipment
The equipment most prominently employed for UV applications are medium pressure Mercury lamps energized through electrodes or microwaves. These lamps are capable of producing typical emission spectrums, generally peaking between 250 and 450 nm. Alterations can be made to the lamps that can shift the spectral output and better match specific inks or coatings that are being cured.
The equipment featured in EB processes consists of electrically operated filaments and grids contained within a vacuum chamber in which electrons are accelerated through a window or foil structure. EB equipment often includes a pumping system to maintain a vacuum in the chamber. Units commonly fall into either “curtain” or “scanning” types, with the “curtain” types used for printing and packaging applications.
Operating Cost and Maintenance
Both UV and EB equipment enjoy the benefit of lower energy costs when compared to traditional drying ovens. When comparing the operating costs of UV to EB, most applications will result in a very similar cost. That said, the cost of the equipment and maintenance does vary between the two methods. The lamps used for UV curing are much less expensive than the equipment needed for EB curing, but it takes more of them to yield the same results. The output of UV lamps will also begin to fade over time, a factor that must be considered to ensure process consistency. Preventive maintenance, such as bulb replacement and reflector cleaning, can go a long way towards prolonging the life of an effective lamp. EB equipment does not experience the same decline in efficiency as UV lamps, but the initial cost is significantly higher. Process cleanliness and temperature control must still be addressed to maintain the EB equipment.
Conclusion
When deciding between UV and EB curing, there are several factors to consider. EB curing can cure ink films that are very opaque, more efficiently than UV. For food packaging and consumer product applications, the absence of Photo Initiators in EB inks reduces odor and the potential for their migration. Pinning or partial cure to affix inks before full cure is not feasible with EB systems. UV cure is suitable for all lengths of print runs while EB is more efficient for longer ones.
Either way, by incorporating UV or EB curing methods, one can be sure to enjoy significantly increased productivity compared to that of the traditional drying methods.
Please note that reasonable effort has been made to review and verify information in this document. Neither Kao Collins and its partners nor the technical reviewers and their agencies assume responsibility for completeness and accuracy of the information or its interpretation. The reader is responsible for making the appropriate decisions concerning their operation, specific materials employed, work practices, equipment, and regulatory obligations. It is imperative to verify current applicable regulatory requirements with state and/or local regulatory agencies.