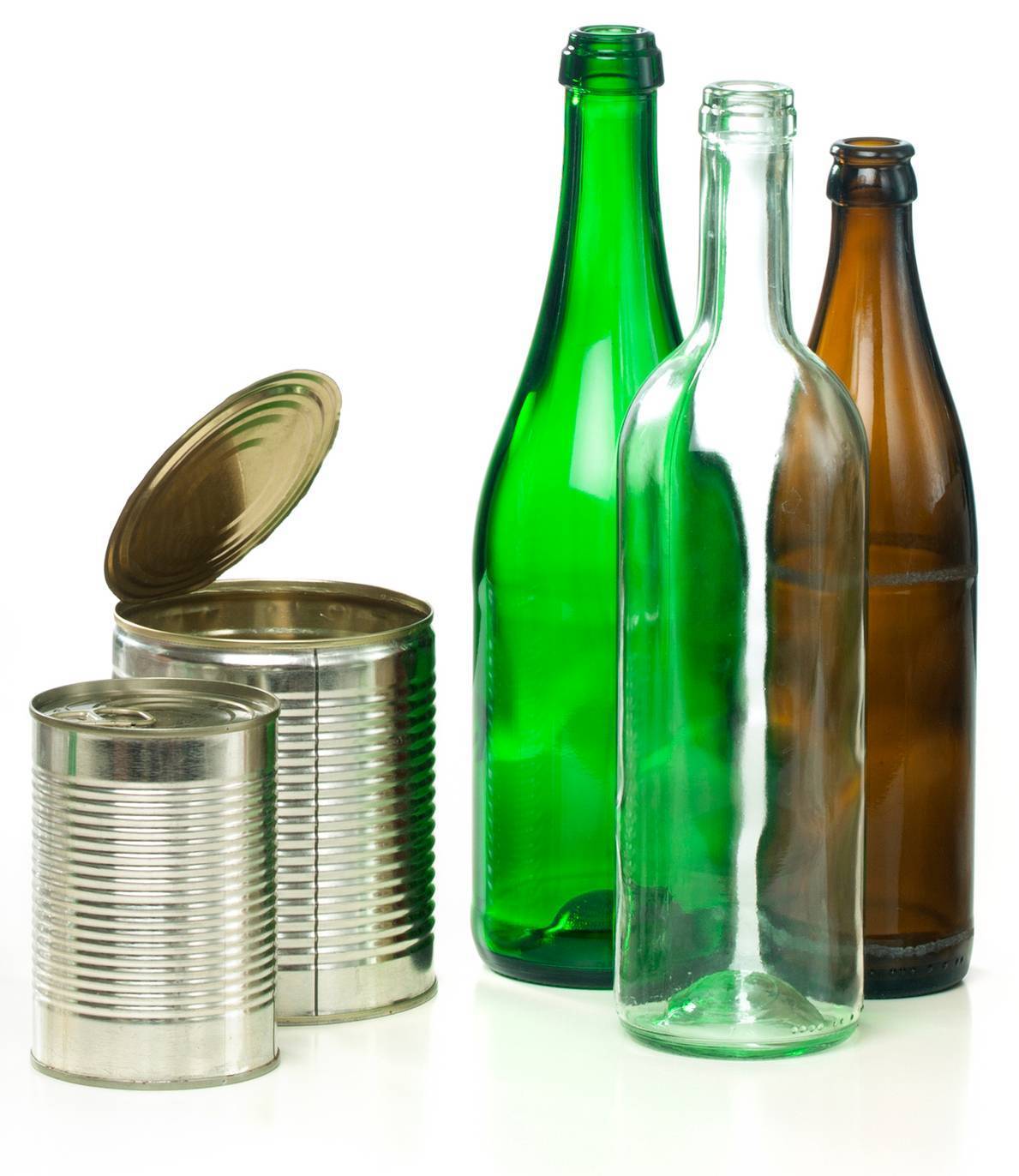
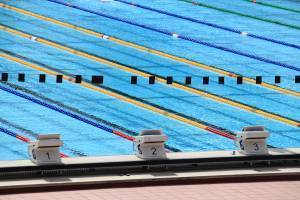
Measuring for ink contaminants is like detecting the presence of a pack of sugar dissolved in an Olympic-size pool.
Walk through any grocery, and you will see many types of packaging–flexible bags, boxes, films, and bottles. The challenge of preventing ink migration from the printed information on food and grocery packaging keeps many chemists, printers, and brand executives awake at night.
It’s easy to understand their anxiety. Some regulations, like the Swiss Ordinance and the Nestlé Guidelines on Food Contact materials, require stringent testing to ensure contaminant levels measure below 10 parts per billion.
For some perspective on how small an amount this is, consider that one pack of sugar in an Olympic-size swimming pool is a concentration of one part per billion. Now think about measuring for that.
To understand how food packaging stays below these contaminant thresholds, we must first understand what ink migration is, what causes it, and what options there are for preventing it.
What is Ink Migration in Consumer Products?
Ink migration is the transfer or bleed-through of ink substances from the packaging material into consumer goods such as food, medicines or health and beauty products. What’s printed on the outside ends up inside.
See Inks for Food Packaging
Get Started
Ink migration is not good for several reasons:
- It puts consumer health at risk
- Changes the flavor and odor of products
- It violates regulations
- It can damage the brand reputation
Added together, that means trouble for the brand, their supply chain partners, and the consumers.
Intentionally Added Compounds
The components of inks–those intentionally-added compounds–can be the most significant source of contamination. These include monomers, antioxidants, plasticizers, and photoinitiators.
Non-Intentionally Added Substances
No less troublesome are the non-intentionally added substances (NIAS), which are difficult to detect and assess after being identified. The sources of NIAS vary.
Understand Global Ink Regulations for Food Packaging
Impurities in the raw materials of the ink may introduce non-intentional substances. Another source may be the by-products of chemical reactions that could happen during packaging, environmental effects during shipping or storage. Consumers may trigger reactions that create dangerous compounds.
The Value of Low Migration Inks
The market for low-migration inks is strong, with pharmaceuticals accounting for 25% of product demand, according to a Global Market Insights, Inc. report. Total revenue could hit $480 million by 2025 compared to $300 million in 2018.
In North America, the market size for low-migration printing inks is projected to grow at over 7% CAGR, according to the market research report.
Types of Ink Migration
Set-off Migration
Ink migration is “set-off” when it transfers from the printed side of one package to the reverse side of another package.
When roll-printed packaging materials are re-wound, the ink may transfer to the reverse side. Similarly, stacking printed cups or other consumer products has the potential to transfer ink to the inside of the cup.
Diffusion Migration
When ink migrates through diffusion, substances pass through the substrate from the printed side of the substrate to contact the food, medicine, or health and beauty product encased in the packaging. The substrate for the consumer product may not block the chemicals in ink. The ink and substrate may interact with environmental conditions to allow migration or introduction of NIAS.
Gas-Phase Migration
Gas-phase ink migration happens when volatile chemicals and compounds in the ink transfer to the interior product through evaporation, or from heating, baking, or boiling food products.
While the primary packaging of consumer products is the obvious source of gas-phase migration, academic studies have confirmed ink compounds used in secondary packaging have migrated through primary packaging.
Ink Migration Barriers
Glass and metal packaging are considered “absolute” barriers. Any ink can be used on the exterior of these packaging materials because these materials prevent migration. Other materials must be evaluated for the potential of ink migration. Both paper and plastic packaging pose a risk of migration.
What Causes Ink Migration or Contamination?
Get informative articles and products in your inbox.
It may be called ink migration, but the ink is only one of the numerous complex factors that contribute to possible product contamination.
Kristin Adams, the marketing manager for Kao Collins, said, “The term low-migration actually defines the selection of materials as well as the ink. So regardless of how an ink is formulated, the ink alone cannot be considered low-migration until it’s actually applied to a specific substrate.”
The following elements must all work in harmony to keep consumers safe and brands protected:
Inkjet Inks
Inks fall into two broad categories.
Direct food contact (DFC) inks must be formulated to meet European and U.S. standards and regulations. They must be non-toxic. These inks are not intended to have any chemical effect on the consumer or the product. M&M’S® and Skittles are printed with a vegetable-based dye ink.
Indirect food contact (IFC) inks don’t contact the food, or health and beauty product. These inks must not pass into the consumer product.
Product packaging relies on low-migration inks, but they are only one part of the equation for preventing contamination. Inks must also be evaluated and tested to identify any external interactions that may produce dangerous contaminants from ink migration.
The U.S. Food and Drug Administration and other regulatory bodies don’t “approve” inks for use in packaging consumer goods. Instead, the FDA approves the materials used in the formulation of inks, and only after extensive testing is submitted.
Packaging Materials
Consumers expect packaging materials to maintain freshness and keep products free of toxic contamination. That’s why testing must ensure the packaging materials and ink choice don’t negatively interact.
The Printing Environment
Contaminants from the equipment used for printing can introduce catalysts that affect either the ink or packaging material–or both. While the ink and packaging material have been verified to prevent dangerous migration, external factors may cause unintended reactions.
Incomplete Curing
Extensive and meticulous ink testing may prove an ink to be safe in ideal conditions. Risk is introduced if the testing conditions are not followed during production. Incomplete curing may introduce toxic materials that would not otherwise exist if the ink had completely dried.
Post-packaging Influences
Environmental conditions introduced during shipping and storage can’t be ignored. The packaging and inks must be tested to meet tolerances of extreme heat, cold, and humidity. In the hands of the consumer, the product must remain safe when boiled, frozen, or heated in a microwave or conventional oven.
Ink Migration in an Eco-Friendly World
Today, manufacturers are using thinner plastics for packaging, which reduces costs and makes less of an environmental impact. Beverage bottles are thinner. Flexible films are replacing cans, glass, and rigid boxes with interior liners. The introduction of new or reformulated packaging materials requires new testing to ensure continued safety.
Packaging Innovations Driving Circular-Economy Movement
Also, brands are turning to bioplastics and other eco-friendly packaging materials in response to customer demands for eco-friendly products to build a circular economy that emphasizes reducing waste and reliance on natural resources. Think of it as supercharged sustainability.
All these new packaging materials must be fully tested to perform with existing or new inks. Kao Collins chemists, for example, work with customers to develop inks for many of these new substrates.
Inks to consider for consumer-product packaging
A wide range of inks is available for the packaging of consumer products in glass or metal containers. Since these are absolute barriers, any industrial inkjet ink that cures to a durable, lightfast, and waterproof finish can be used. UV-curable and LED-curable inks are good options.
Solvent inks, especially Kao Collins SIGMA solvent ink for HP 45 technology, is an optimal choice for printing coding, marking, and barcodes. It performs exceptionally well on foils, plastics, metals, and flexible films. A significant benefit of this new ink is the 12-hour decap, which offers more flexibility on the production line.
Other packaging requires more research and testing to meet the safety requirements discussed earlier. Low-migration UV-curable and LED-curable inks are often used. Water-based inks and soy-based inks can also be included in the mix.
Kao Collins produces industrial inkjet inks for TIJ, PIJ, and CIJ technologies. Explore the inks available for the leading printhead technologies. Custom solutions can be formulated for testing on the new packaging materials that are being researched and produced. Contact Kao Collins.
Frequently Asked Questions – FAQs
What is ink migration?
It is the transfer or bleed-through of ink substances from the packaging material into consumer products such as food, medicines or health and beauty. What’s printed on the outside ends up inside.
What are the types of ink migration
Set-off migration – The ink transfers from the printed side of one package to the reverse side of the substrate where it comes in contact with the consumer product.
Diffusion migration – Ink substances pass through the packaging material from the printed side of the substrate, where it comes in contact with the food.
Gas-phase migration – Volatile chemicals and compounds transfer to the interior through ink evaporation, or from heating, baking or boiling food products.
What are the risks of ink migration?
It puts consumer health at risk. It can change the flavor, odor, or performance of a product. It violates regulations, putting the brand at risk.
What are non-intentionally added substances in inks (NAIS)?
These are impurities in the raw materials of the ink. Another source may be the by-products of chemical reactions that could happen during packaging, environmental effects during shipping or storage. These are of considerable concern for the industry.
What is “food-grade” ink?
Ink is called “food-grade” if it is safe for human consumption and can come in direct contact with food. For the ink to be actually used, there must be testing for it to be considered “food-safe.”
What is a functional barrier for consumer-product packaging
It is a substrate, after tested usage, that prevents the migration of ink, from coming in contact with the product. Testing conditions include the ink formulation, packaging material composition, time exposure to the ink, and environmental factors.