Nov 20, 2024
How the Printing Industry is Adapting to Compliance Pressures Beyond 2025
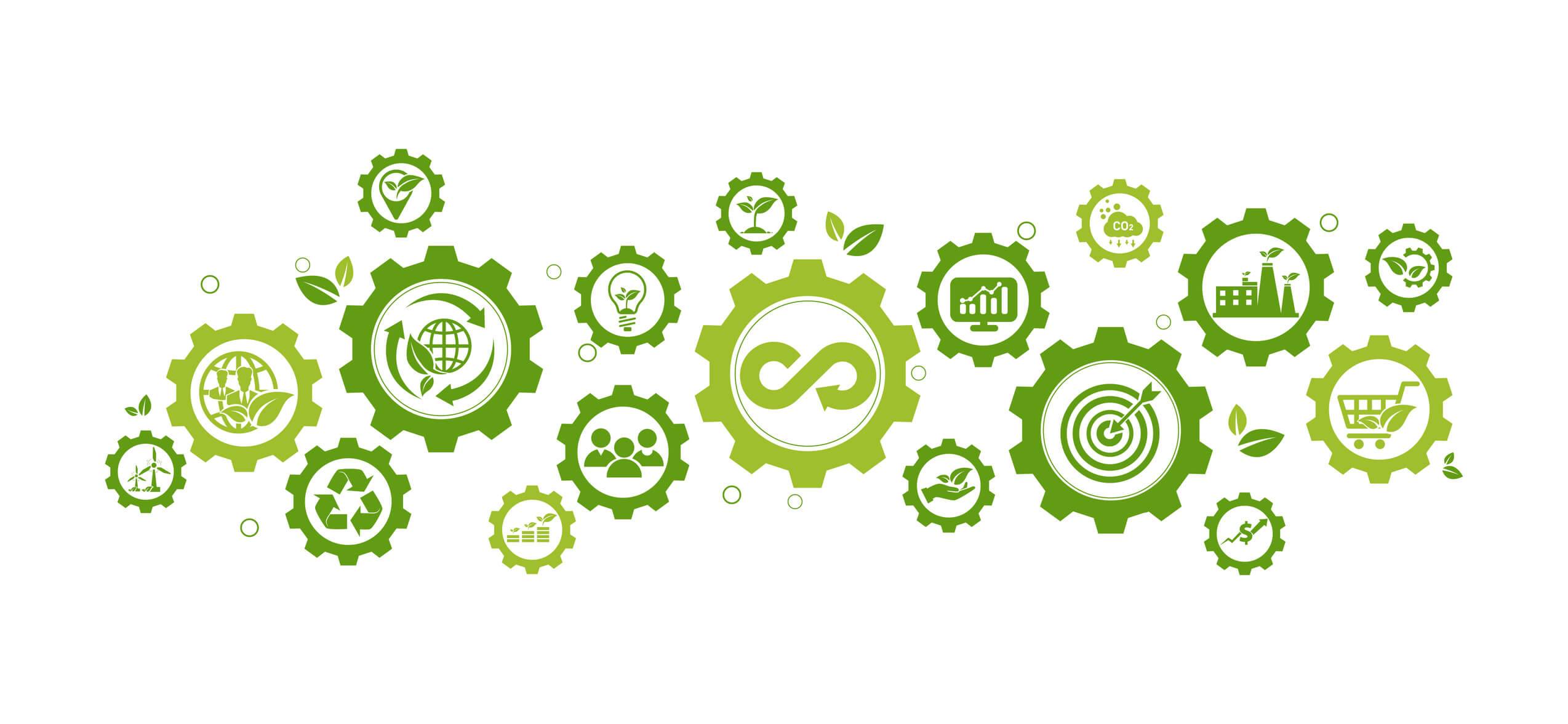
The commercial and industrial printing industry continues to navigate through stringent health and environmental regulations. The Clean Air Act (CAA) and the National Emission Standards for Hazardous Air Pollutants (NESHAP) set rigorous standards for reducing harmful emissions.
Additionally, upcoming regulations are introducing even stricter controls on chemicals and practices within the industry.
Regulations and industry self-policing tied to Extended Producer Responsibility, which requires manufacturers to manage the entire product lifecycle, can snare the whole production chain, including printing.
This article examines existing and likely regulations and highlights why industrial inkjet printing is exceptionally well-suited for the industry in 2025 and beyond.
Stringent MACT Standards Reshaping the Printing Industry
The Clean Air Act (CAA) includes requirements affecting the printing industry, such as limits on volatile organic compounds (VOCs) and hazardous air pollutants (HAPs).
These regulations require printing facilities to meet air quality standards, often through costly control systems. Printers have flexibility in choosing the specific technologies and practices to achieve compliance.
It’s a given that the regulatory landscape for the printing industry is expected to become tighter, as is the case with the Maximum Achievable Control Technology (MACT), the standard set by the U.S. Environmental Protection Agency (EPA) under the National Emission Standards for Hazardous Air Pollutants (NESHAP).
With MACT, best-performing facilities set the minimum compliance standard.
The bar moves higher as companies improve equipment and ink chemistry to reduce emissions. The standards set specific emission limits for organic HAPs, including pollutants like xylene, toluene, ethylbenzene, methyl ethyl ketone, methyl isobutyl ketone, methanol, ethylene glycol, and certain glycol ethers.
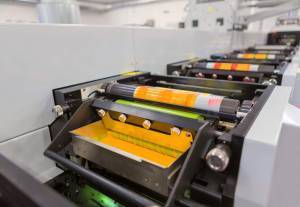
Traditional flexo and rotogravure printing face rising costs and complexity to meet emissions standards.
Traditional flexo and rotogravure printing operations using solvent-based inks for films and glossy substrates must invest in more costly and aggressive MACT technology, giving industrial inkjet printing an advantage.
This creates an operational and financial burden for these facilities as they continuously upgrade their control technologies to comply with new emissions benchmarks. Facilities must invest in advanced pollution control equipment such as thermal oxidizers and carbon adsorption systems and adopt rigorous best practices for minimizing emissions during printing and cleanup processes.
In contrast, low VOC water-based or UV-curable inkjet inks generally contain fewer hazardous air pollutants (HAPs) than solvent-based ones utilized in traditional printing processes.
“By prioritizing environmental sustainability through rigorous research and development, we’ve optimized our water-based ink formulations to enhance print quality and durability on more substrates, including non-porous surfaces, while minimizing the environmental impact of the printing process,” said Curtis Soller.
Furthermore, even solvent-based inkjet inks in cartridges minimize emissions, Curtis Soller said.
The transition to inkjet printing simplifies regulatory compliance and diminishes the necessity for extensive pollution control measures, making it a more cost-effective and sustainable option.
Printing Industry Braces for Impact as HFC Phase-Down Accelerates
The printing industry, notably analog operations, will be further buffeted by hydrofluorocarbons (HFCs) phase-down under the American Innovation and Manufacturing (AIM) Act.
The required reductions started in 2019, with a second step in 2024. The remaining reduction milestones arrive in 2029, 2034, and 2036, when the target of an 85% reduction is expected to be achieved.
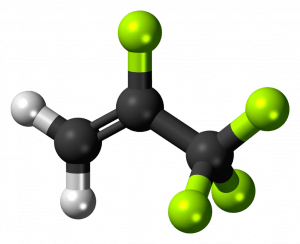
Restrictions on HFCs push printing companies toward tech shifts, mergers, and eco-friendly innovations, impacting profits but opening doors to sustainable market opportunities.
Hydrofluorocarbon (HFC) emissions regulation aims to lessen climate impact by limiting the use of these greenhouse gases. They have a high global warming potential (GWP) and retain considerably more heat in the atmosphere than carbon dioxide.
As HFCs are phased out, companies using HFC chillers must shift to alternatives for cooling fluids, preventing equipment overheating, maintaining efficiency, and ensuring quality.
The phase-out of HFCs creates challenges and significant adjustments.
Required HFC reductions put some printing companies using solvent recovery systems behind the eightball. Until now, companies have used HFCs in solvent recovery systems to reduce waste and minimize environmental impact. As HFCs continue to be phased out, companies must find alternatives for solvent recovery.
Replacing HFCs in chillers and solvent recovery systems means printing plants must adapt quickly.
Potential Effects on Printing Companies
Closures: Companies might shut down rather than invest in new technologies.
Mergers: Companies may merge or acquire other companies to scale production and share costs.
Technology Shifts: Turning to alternative technologies, such as industrial inkjet printing, can be more environmentally friendly and less expensive.
Profit Margins: New equipment and training affect the bottom line.
Innovation and Adaptation: Companies may gain a competitive advantage and enhance their reputation as sustainable businesses.
Market Opportunities: There may be new market opportunities for companies that develop and offer environmentally friendly solutions and technologies.
EPR Laws Challenge Print Service Providers and Manufacturers
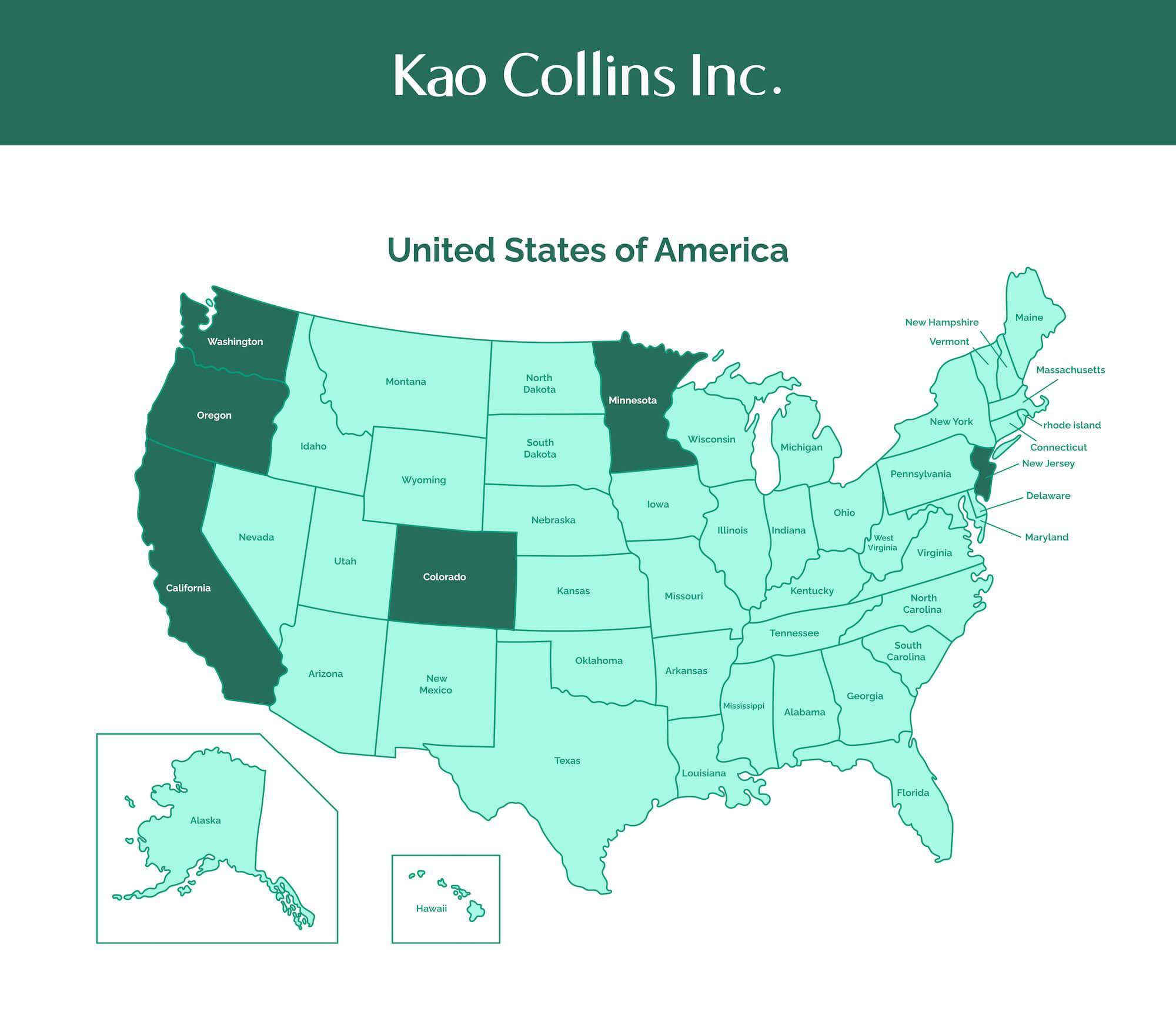
Maine was the first state to have an Extended Producer Responsibility (EPR) law.
The cloudy future of regulation and compliance is taking shape in the form of EPRs, which require manufacturers to take responsibility for the entire lifecycle of their products, including responsible disposal and recycling of packaging and production materials.
The first Extended Producer Responsibility (EPR) was signed into effect in July 2021. The Maine law places responsibility for recycling and managing packaging waste on producers rather than municipalities. Since then, six other states, including California, Colorado, Oregon, New Jersey, Minnesota, and Washington, have enacted EPR laws.
The regulation could have a trickle-down effect that can ensnare print service providers.
A manufacturer looking to achieve mandated waste reduction and fees may redesign packaging to use materials that are easier to recycle or reuse. This may force printers to begin using biodegradable or other eco-friendly ink formulations.
Printers may need new production systems or to modify machinery to handle new materials and designs.
Ink manufacturers will face increasing pressure to develop less harmful formulations to the environment, and they may need to certify that inks meet regulatory requirements.
Finally, inks used on packaging must be easily removable during recycling to ensure the packaging material can be effectively recycled. Regulations may also require inks to be non-toxic and free from harmful chemicals to reduce environmental impact.
Companies are already identifying an opportunity in this space.
One example of innovation in this area is Kao Corporation’s development of a deinking thermo switch polymer that enhances the recycling of flexible packaging materials.
These advancements align well with Extended Producer Responsibility (EPR) regulations, enabling more efficient recycling processes.
The innovation started about three years ago to create a primer to improve ink adhesion.
The deinking technology uses variations in water temperature to initiate a chemical reaction. Heat causes a polymer integrated into the ink to shift from adhering to the flexible film to actively repelling it.
“This breakthrough makes recycling flexible packaging significantly easier and more efficient. It’s a game-changer for the industry and a big step forward in our commitment to sustainability,” said Marc Granero, inkjet sales manager at Kao Chimigraf.
Implementing EPR laws marks a significant shift in the regulatory landscape, requiring manufacturers to take full responsibility for their product’s lifecycle. The pressure on print service providers and ink manufacturers to comply with these standards will undoubtedly drive innovation and collaboration within the industry.
Eco-Friendly Innovations Shape the Future of Printing
Printers and manufacturers face challenges on multiple fronts. Vocal consumers are compelling companies to embrace eco-friendly solutions. And, governments push stricter regulations to achieve health, climate, and air quality goals.
Navigating this minefield involves adopting innovative technologies and ink formulations that enhance sustainability, efficiency, and competitive advantage.
Contact Kao Collins about eco-friendly inkjet inks.